All companies need to enhance, or at the very least they need to achieve this consistently to be aggressive. Complacency may really feel good within the second, however that second rapidly passes, particularly within the enterprise world. Don’t be left behind. The query is how can one improvethe operations of a enterprise to make it extra environment friendly and worthwhile? There are various solutions, from academic and bodily health to spirituality. However is there a unifying concept of course of enchancment, and in that case, can or not it’s sustained?
Have you ever heard of the kaizen methodology? It’s a set of rules and methods for steady enchancment that helps organizations throughout industries be extra productive. However earlier than we dive into it, let’s start by defining the Japanese phrase “Kaizen.”
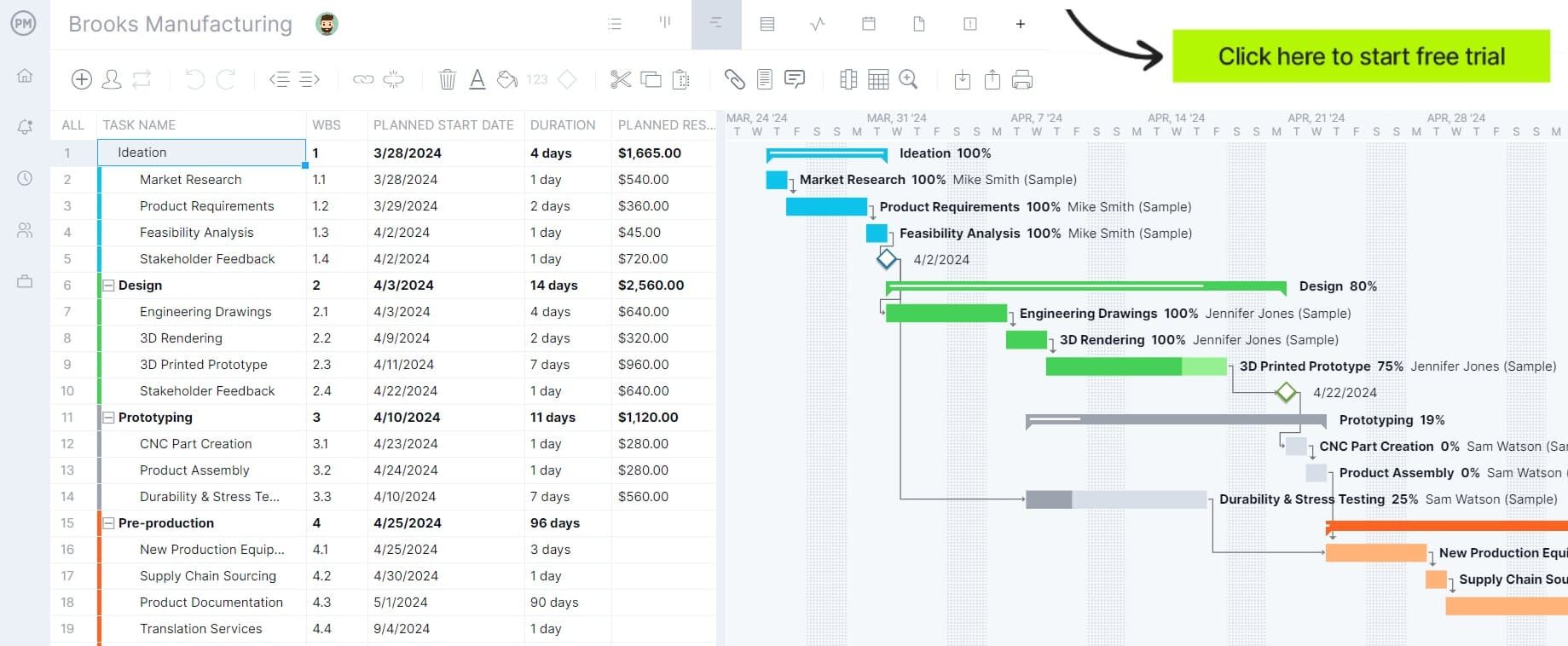
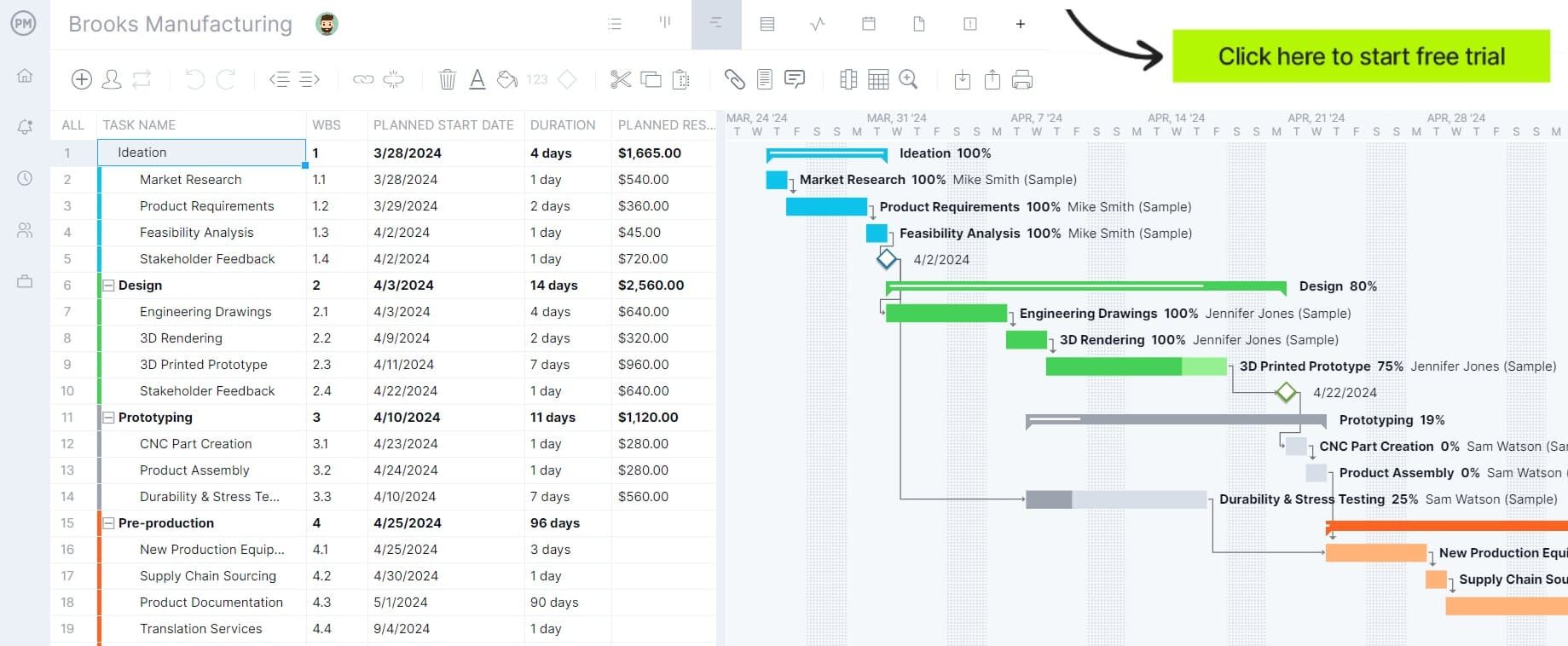
What Is Kaizen?
Kaizen means enchancment, however extra than simply that, it means continuous enchancment for your online business operations. Enchancment that’s not reaching past what it could actually at present do is static.
Kaizen, extra exactly, means change for the higher (kai is change and zen is for the higher). When it comes to enterprise, kaizen signifies that all actions have to be repeatedly bettering. Meaning the whole lot within the group, from workers to the CEO. However it’s not simply making use of to personnel, processes are additionally included.
The thought was codified by Masaaki Imai, an organizational theorist and administration advisor, over 30 years in the past with the publication of this e book, Kaizen: the Key to Japan’s Aggressive Success. Since then, the implications have reached past business and the kaizen rules have been used to assist in healthcare, psychotherapy, authorities, banking and even life teaching.
The kaizen methodology works at fixed enhancements via the elimination of waste. It’s been round in Japan since after World Struggle II, although influenced by high quality administration concepts from america. It’s a part of The Toyota Method, which is a set of rules that assist the corporate’s administration strategy to manufacturing.
What Is the Kaizen Methodology?
Kaizen is a steady enchancment philosophy to extend the effectivity of enterprise operations, rooted in Kaizen rules resembling eliminating waste (muda, mura, muri), standardizing enterprise processes via the 5S system, and utilizing the Plan-Do-Test-Act cycle to implement operational and organizational planning modifications.
Kaizen is a technique that emphasizes bottom-up administration, empowering workers in any respect ranges to establish issues, supply their enter and take part in fixing them.
Practices like Gemba Walks encourage firsthand remark of worker efficiency and operations, whereas centered Kaizen occasions goal speedy course of enhancements. Collectively, these instruments and mindsets foster a tradition of effectivity, teamwork and long-term operational excellence via small, incremental modifications that drive significant progress and lasting outcomes over time.
Let’s now outline every of the weather that make up this steady enchancment methodology.
Kaizen Rules
A philosophy centered on steady, incremental enchancment in all areas of life, particularly within the office. It emphasizes small, constant enhancements over time to realize bigger long-term positive aspects.
Kaizen Waste Varieties (Muda, Mura, Muri)
Muda refers to waste in any kind that doesn’t add worth, resembling extra manufacturing or time spent on non-essential duties. Mura is unevenness or inconsistency in processes, usually resulting in inefficiency or pointless stress. Muri refers to overburdening individuals, tools or processes past their capability, which may trigger breakdowns or fatigue.
Kaizen Gemba Stroll
A apply the place managers and crew members go to the “Gemba” (the precise place the place work is finished) to look at processes, perceive challenges and collect insights straight from the individuals concerned within the work.
Kaizen 5S System
A strategy for organizing the office to extend effectivity and scale back waste. The 5S rules are: Kind (seiri), the elimination of pointless gadgets; set so as (seiton), arrange gadgets for simple entry; shine (seiso): clear the work space; standardize (seiketsu): set up constant processes. maintain (shitsuke), preserve the enhancements.
Plan-Do-Test-Act (PDCA)
A steady enchancment cycle used to check and implement modifications. It entails planning a change (plan), implementing it (do), checking the outcomes (examine), and taking motion based mostly on the outcomes (act).
Backside-Up Administration
A administration strategy the place selections are
made with enter from lower-level workers, encouraging their involvement and fostering a way of possession in enchancment initiatives.
Kaizen Occasions
Targeted, short-term actions the place a cross-functional crew works intensively to make vital enhancements to a selected space, usually utilizing the Kaizen rules.
Kaizen Board
A software for visualizing and monitoring the standing of enchancment
initiatives. It sometimes shows an inventory of ongoing, deliberate and accomplished tasks or concepts, serving to groups keep aligned and clear of their enchancment efforts.
Kaizen Rules
The 5 rules of kaizen are basic to any software of kaizen.
- Know Your Buyer: Data of who your promoting a services or products to is how one creates worth. It’s key that firms establish their buyer’s pursuits to boost their expertise.
- Let It Circulation: This is applicable to the goal of attaining zero waste. It could be an unimaginable purpose, however that’s kaizen for you: if you happen to may obtain that goal enchancment would cease. Due to this fact, everybody within the group is working in the direction of eradicating any waste from their nook of the enterprise whereas additionally within the course of creating worth.
- Go to Gemba: The literal translation for gemba is “the actual place.” On this context, it’s about management and figuring out what is occurring at each stage of the group. You’ll be able to consider it as following the motion, as worth is created the place one thing is definitely taking place. That’s the place you need to be.
- Empower Folks: This one is directed in the direction of groups and having them organized in such a approach that it helps the kaizen rules. Due to this fact, management should set targets for his or her groups that aren’t contradictory. They need to supply a system and instruments to assist the groups obtain these targets.
- Be Clear: Information is the strongest figuring out issue. It’s the metric that measures success. Due to this fact, efficiency and enhancements have to be tracked with actual information
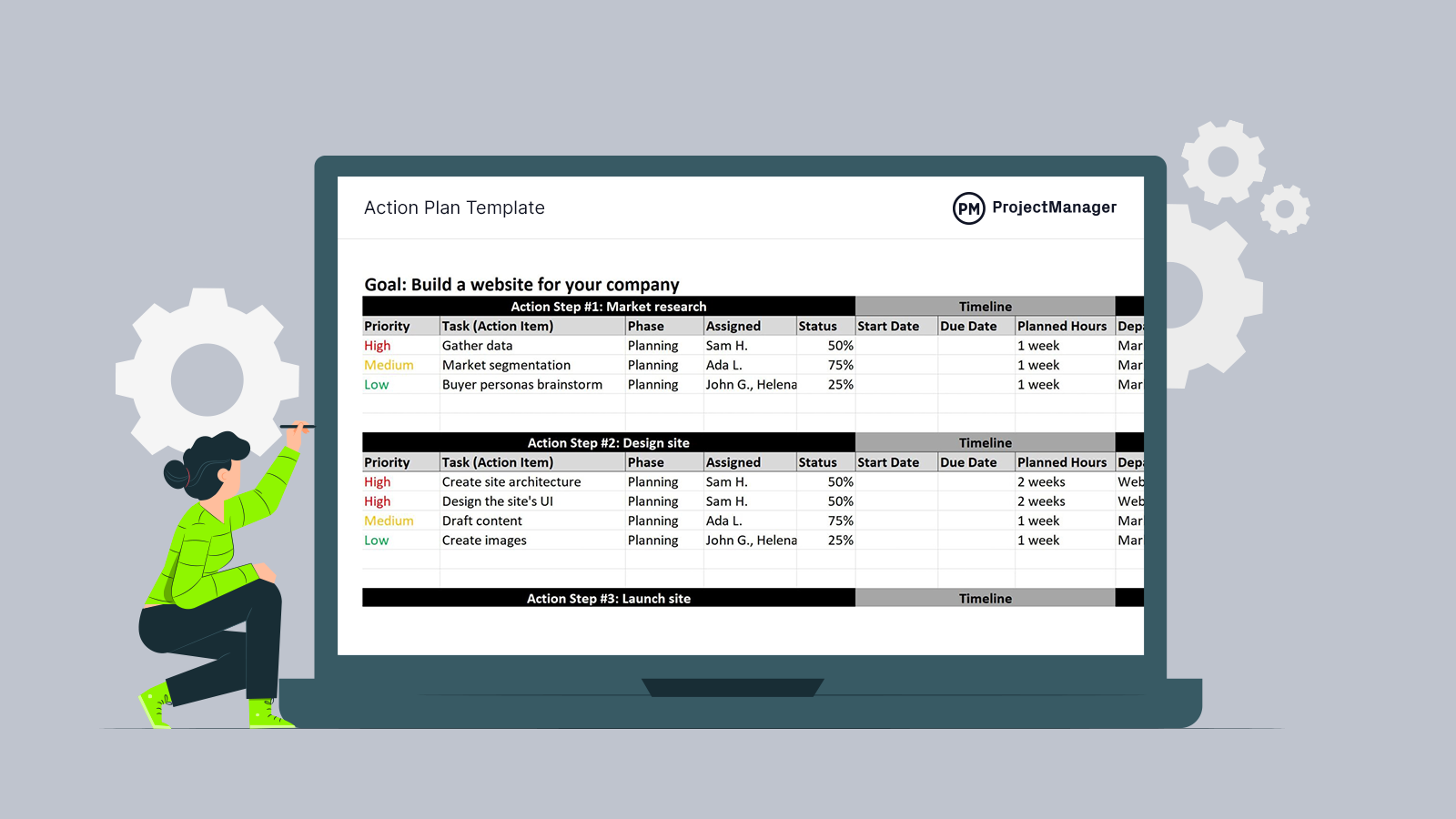
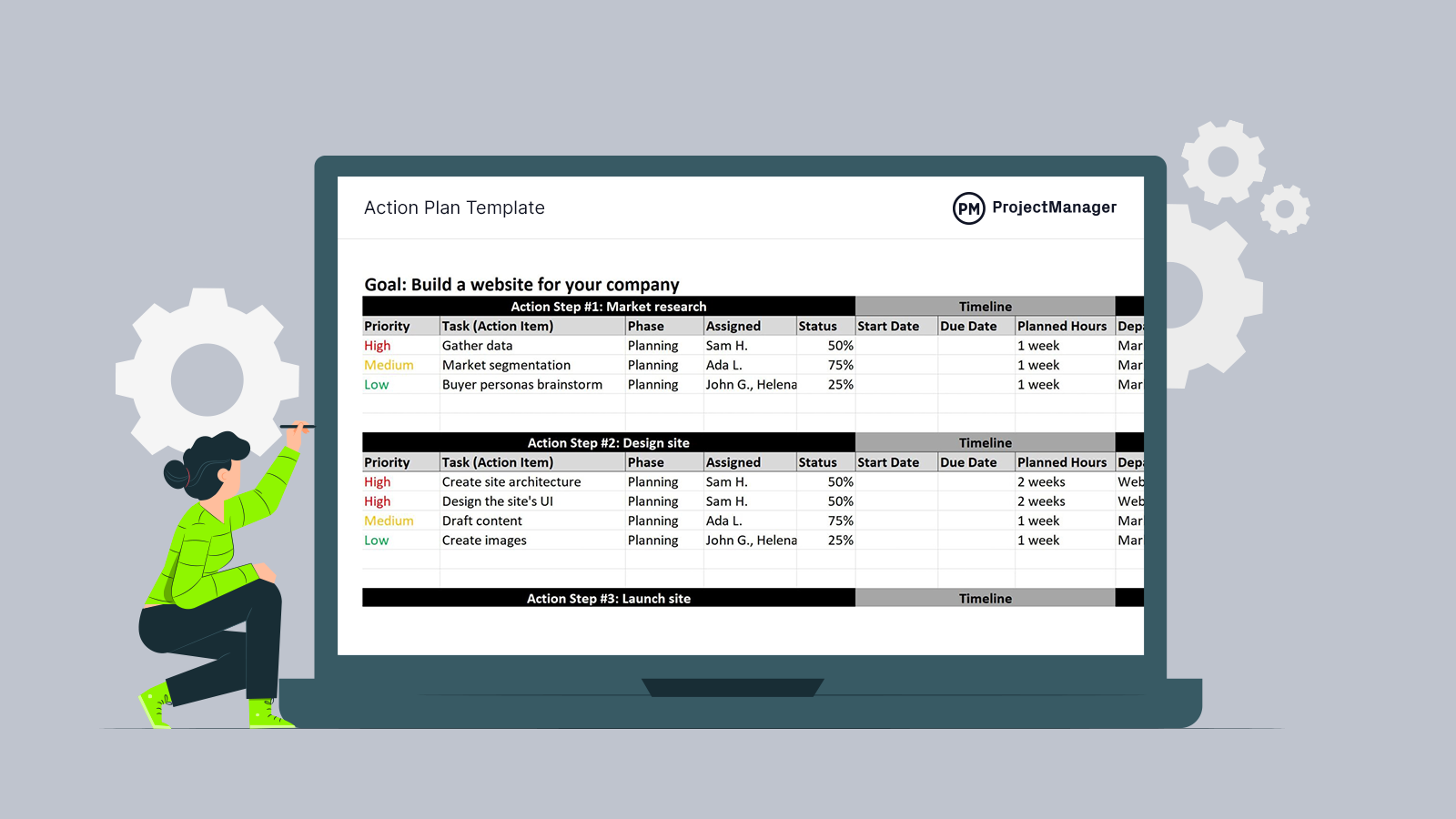
Get your free
Motion Plan Template
Use this free Motion Plan Template to handle your tasks higher.
Get the Template
Kaizen in Motion: Sensible Suggestions
The rules are the guiding lights; the motion plan is the place kaizen hits the highway operating. It’s all about organizing, in order that the main focus is at all times on enchancment and its targets are each a part of the group. Everyone seems to be a part of the method. A constant software of the kaizen motion plan results in steady enchancment.
First, take every nook of your group and have a look at methods it may be improved. This may contain crew collaboration and whole involvement from everybody. People want autonomy to take motion on enhancements themselves, which builds a tradition of engagement. That is completed with a seamless stream of solutions after which implementing them to enhance the group.
Every occasion is printed by the acronym PDCA, which stands for plan, do, examine, act. Start by setting targets, with documentation and background. Then overview what the present state is with that a part of the enterprise and plan in the direction of bettering it. Establish what enhancements will likely be carried out and try to repair what isn’t working. Report the outcomes, observe up and repeat.
The thought of at all times making small enhancements will not be dissimilar to lean manufacturing, particularly with the emphasis of eliminating waste. Kaizen, like a lean or agile strategy, works with iterations. It retains firms versatile.
How Kaizen and ProjectManager Work Collectively
Concepts are nice and methodologies are basic to implementing these concepts. However the very best plans of mice and males usually go astray in the event that they don’t have a challenge administration software to trace their progress. ProjectManager is a dynamic and nimble software program that cashes the examine that kaizen writes.
ProjectManager has Kanban Boards to Monitor Progress
What ProjectManager.com supplies is a method to monitor that enchancment. Kanban is one other Japanese work, which interprets as signboard or billboard. It additionally grew from the Toyota Method of producing, providing a visible workflow that enhance efficiencies by ensuring that the provides you want now are at all times available, however no more than have to be saved.
It’s a sublime system of columns and playing cards. Every column can have a to do, doing and completed heading. Beneath every of these column headings are playing cards, which seize the person job. These playing cards are then moved from column to column as they’re recognized, labored on and accomplished.
These boards are an effective way to trace the progress of the enhancements. With ProjectManager.com, the kanban boards are much more helpful, as they are often assigned to particular crew members or a complete group. Then, as a result of the software program is on-line, as groups replace their standing that data is immediately mirrored throughout the software program.
ProjectManager’s Actual-time Dashboard Tracks Progress
Kaizen encourages collaboration and ProjectManager helps teamwork by giving groups a platform to speak on the job stage. Paperwork and pictures may be hooked up to the cardboard within the board view of our software program, so these essential information are straightforward to entry. There’s a dialog field to dialogue with different crew members. When a remark is added, all these assigned the duty are notified. It’s particularly useful in case your groups are distributed on completely different websites.
However groups aren’t the one ones who profit from ProjectManager. Simply as kaizen entails the entire group in making steady enhancements, ProjectManager additionally provides managers the instruments they should assign simply and monitor the progress of the enhancements as they’re carried out.
Whereas challenge managers can view the progress of the kaizen implementation on the kanban board, they in all probability are going to need extra detailed data. ProjectManager has a real-time dashboard that collects all the info crew members enter after which crunches these numbers right into a sequence of challenge metrics which are displayed multi functional place.
The actual-time dashboard has colourful and straightforward to learn graphs and charts that monitor progress, workload, timelines and extra. These may be shared or printed out for presentation. However in ProjectManager.com, the graphs and charts may be filtered to point out simply the quantity of information you want. This implies when a challenge supervisor is discussing gadgets with the crew, they’ll go deep into the info, but when the stakeholders want a extra normal overview, that may be displayed in a click on.
Kaizen and ProjectManager.com are a match made in challenge administration heaven. However ProjectManager can achieve this far more than allow you to implement change. Our cloud-based challenge administration software program can plan, monitor and report on any type of challenge. On-line Gantt charts make scheduling collaborative and groups love our easy-to-use job lists and timesheets. See how ProjectManager can enhance your challenge administration right this moment by taking this free 30-day trial.